In today's business environment, the need for efficient and speedy product development has increased significantly. As companies strive to lead the market, advanced manufacturing techniques are essential. Rapid injection molding has emerged as a breakthrough in this arena, allowing businesses to transform their visions to life with extraordinary speed and precision. This technology is not just about production; it is about changing the way products are conceived, developed, and fabricated.
The beauty of rapid injection molding lies in its ability to enhance the entire production process. By minimizing lead times and lowering costs associated with traditional manufacturing methods, it enables companies to evaluate and iterate designs more freely. This means that businesses can adapt to market needs faster, ultimately better products and greater customer satisfaction. As we examine the revolutionary impact of rapid injection molding , we will find out how it is changing the field of product manufacturing and fueling innovation across industries.
Benefits of Fast Injectable Manufacturing
Rapid injectable molding offers a significant reduction in lead times compared to conventional methods. By leveraging advanced techniques and technologies, manufacturers can produce parts swiftly, allowing for faster prototyping and product iterations. This speed is crucial in the modern competitive market, where being able to bring a product to market rapidly can be a critical factor for success.
Another advantage of quick injectable manufacturing is its affordability for small production runs. Unlike traditional injectable molding, which often requires high upfront investments in tooling and set-up, rapid injection molding allows for reduced initial costs. This makes it available for startups and companies looking to test new ideas without investing to large-scale production right away.
The versatility of fast injectable molding cannot be overlooked. It allows for the rapid adjustment of designs and materials, enabling manufacturers to implement changes on the fly. This adaptability not only streamlines the product development process but also ensures that the final product aligns with market demands and quality standards, improving customer satisfaction and driving innovation.
Applications in Various Fields
Fast injection molding has become crucial across different industries due to its ability to streamline production operations. In the car sector, manufacturers utilize this technology to create intricate components efficiently and effectively. The potential to produce top-notch prototypes and small production runs allows car makers to test and improve designs before committing to mass production, reducing both time and costs markedly.
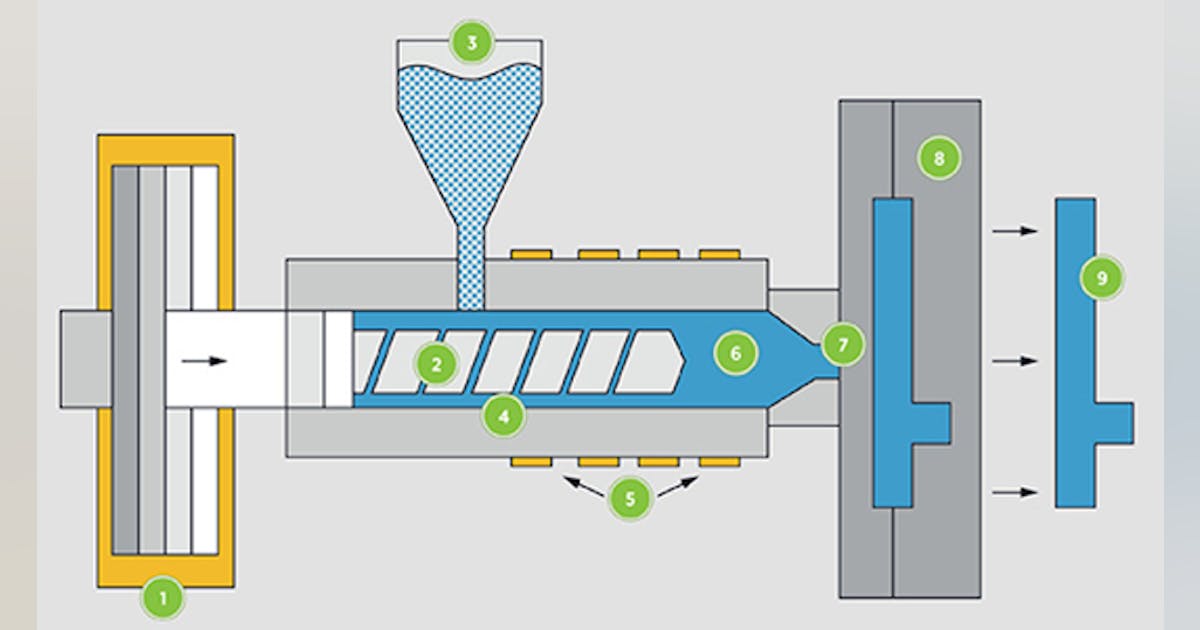
In the electronics industry, rapid injection molding is key in hastening product launches. Companies can produce intricate parts such as casings and internal components in a fraction of the time compared to conventional methods. This quickness enables companies to adapt quickly to market demands and adjust to swiftly changing consumer preferences, ensuring that they remain aggressive in a fast-paced environment.
The healthcare industry also gains greatly from rapid injection molding, especially in the production of devices and instruments. With demanding regulatory requirements, the need for precise and consistent components is essential. Fast injection molding allows for the creation of customized medical devices tailored to specific needs, which can be produced swiftly while maintaining the required quality standards. This not only improves patient care but also allows healthcare providers to develop and improve their offerings effectively.
Emerging Innovations in Product Evolution
As fields continue to seek efficiency and quickness in product production, fast casting formation is poised to play a key role in shaping the future of item creation. Businesses are more frequently integrating advanced technologies such as artificial intelligence and automated learning into their manufacturing processes. These advancements allow for enhanced data analysis, optimizing concept iterations, and improving quality control in quick casting. This trend not only minimizes delivery times but also improves the capability to adapt quickly to market demands.
Environmental responsibility is becoming a central focus for producers as environmental concerns increase. Fast casting can assist significantly to sustainable practices by lessening material waste and power usage. The use of bio-based and recyclable materials in the molding process aligns item evolution with eco-friendly initiatives. As an increasing number of companies commit to sustainability, the application of fast molding will likely increase, fueling creativity while addressing green issues.
Personalization is another upcoming shift that will affect item evolution. Rapid injection allows personalized products, enabling producers to develop items that meet exact client requirements more quickly than standard techniques. This shift towards tailored products signifies a transition away from generic solutions, allowing for increased consumer engagement and contentment. As tools improves and production methods evolve, the demand for customized items will increase, making quick molding an integral tool in current production practices.